Quality Assurance Division
G3 Engineering Consultants (Pvt.) Ltd. has established, documented, implemented, maintains and continually improves
a quality management system covering the requirements of ISO 9001:2000.
To implement the quality management system, the company has managed to:
- Identify the processes needed for the quality management system;
- Determine the sequence and interaction of these processes;
- Determine criteria and methods required to ensure the effective operation and control of these processes;
- Ensure the availability of information necessary to support the operation and monitoring of these processes;
- Measure, monitor and analyze these processes
- Implement actions necessary to achieve the planned results and continual improvement.
G3 Engineering Consultants (Pvt.) Ltd. has prepared its quality management system documentation, which includes:
LEVEL 1: QUALITY SYSTEM MANUAL
Quality System Manual is a top level policy document outlining the structure and general principles of the quality management system. It includes:
Quality System Manual is a top level policy document outlining the structure and general principles of the quality management system. It includes:
- The scope of the quality system, including details of and justification for any exclusion
- Reference to the Quality System Procedures, Standard Operating Procedures or related documentation
- A description of the sequence and interaction of the processes included in the quality management system
LEVEL 2: QUALITY SYSTEM PROCEDURES (QSP)
The Quality System Procedures are the second level quality system documents, which contain a detailed description of how quality system requirements, as specified by ISO 9001:2000 standard, have been addressed and implemented in various functions of the division. The Quality System Procedures serve as an operational guide for all the concerned departmental staff to ensure that operations are carried out in a controlled and systematic manner as per quality system requirements. Controlled copies of Quality System Procedures are distributed to all the concerned persons in the controlled distribution list, given on the first page of the each procedure.
LEVEL 3: STANDARD OPERATING PROCEDURE (SOP)
The SOP are third level quality system documents, which contain instructions for individuals to perform routine tasks or specific functions. SOP are prepared by the related section incharge, reviewed by concerned departmental head and approved by Director Technical. The SOP is then distributed where required. Quality Management Representative (QMR) maintains the distribution status of SOP on the Master List of Documents.
LEVEL 4: REFERENCE REGULATIONS, EXTERNAL DOCUMENTS, STANDARDS AND RECORDS
These are fourth level quality management system documents, which include records required in the Quality Management System of organization. These are properly referenced in all the relevant procedures, and include data/records such as test reports, forms, log sheets and other reports generated while performing routine activities.
These include all the legal and regulatory requirements that apply to various aspects of the software products or services.
CUSTOMER SATISFACTION
G3 has determined and established processes for monitoring information on customer satisfaction and/or dissatisfaction to assess whether the division has met the customer requirements. The methods and measures for obtaining this information and its use are defined in the relevant procedures. Define appropriate procedures.
Examples include: customer and user surveys, communicating directly with customers need assessments and analysis of data, reports from customers, collection of data from different sources.
INTERNAL AUDIT
The internal audit process acts as a management tool for independent assessment of any designated process or activity. The internal audit process provides an independent tool for use in obtaining objective evidence that the existing requirements have been met. Technology Division has established a process for performing internal audits in order to determine if the quality management system:
Conforms to the requirements of this international standard
Has been effectively implemented and maintained
Technology Division plans audit program, which is based on the status and importance of the activities, areas or items to be audited, and the results of previous audits.
Technology Division has documented and implemented for internal audit that covers the audit scope, frequency and methodologies, as well as the responsibilities, requirements for conducting audits, recording and reporting results to management. Audits are performed by personnel other than those who performed the work being audited. The management of the division takes timely corrective actions on deficiencies found during audit. Follow up actions include the verification of the implementation of corrective action and the reporting of verification results.
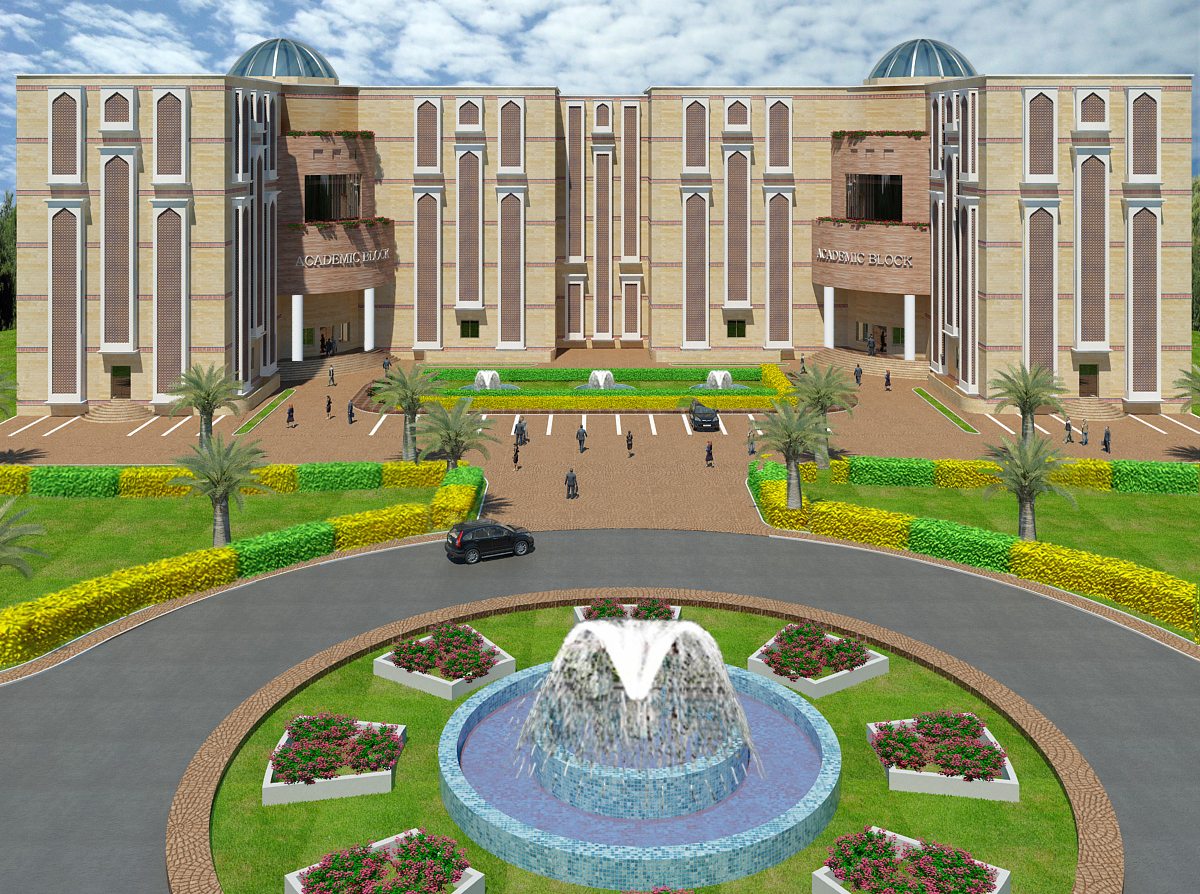